Waterproof LED Strip Lights: Everything You Need to Know
Table of Contents
When it comes to lighting solutions, LED strip lights have become a popular choice for their versatility, efficiency, and sleek design. However, not all environments are created equal, and specific installations require more than just standard LED strips. This is where waterproof LED strip lights come into play. Whether you’re looking to illuminate outdoor spaces, bathrooms, or areas prone to moisture, waterproofing is crucial to ensure the longevity and performance of your lighting setup. In this blog post, we’ll delve into the importance of waterproofing in LED strip installations and explore IP ratings to help you make an informed choice.
Importance of Waterproofing in LED Strip Installations
Waterproofing is an essential factor when installing LED strip lights in environments exposed to moisture, humidity, or direct water contact. Without proper waterproofing, LED strips can suffer from water ingress, leading to short circuits, reduced brightness, or complete failure. This not only compromises the effectiveness of your lighting but can also lead to costly repairs or replacements.
In outdoor settings, such as garden paths, patios, or under-eave lighting, waterproof LED strips ensure that your lights can withstand the elements, including rain, snow, and even dew. Similarly, in indoor areas like kitchens, bathrooms, and wet rooms, waterproof LED strips protect against steam, splashes, and accidental spills, providing peace of mind and reliable performance.
By choosing waterproof LED strip lights, you’re investing in durability and safety, ensuring that your lighting remains functional and practical, regardless of the conditions.
Overview of IP Ratings and What They Mean
When selecting waterproof LED strip lights, understanding IP ratings is crucial. The IP (Ingress Protection) rating system is an international standard that classifies the degree of protection provided by electrical enclosures against the intrusion of solid objects, dust, and water. An IP rating typically consists of two numbers:
- The First Digit Indicates the level of protection against solid objects and dust (ranging from 0 to 6).
- The Second Digit Represents the level of protection against water (ranging from 0 to 9). Here is a breakdown of what these numbers mean for waterproof LED strip lights:
1. IP20 – Basic Protection:
- Protection against solid objects larger than 12.5mm (e.g., fingers), but no protection against water.
- Suitable for indoor use in dry areas.
2. IP54 – Splash Proof:
- Protection against solid objects over 1mm (e.g., wires) and splashes of water from any direction.
- It is ideal for areas like kitchens or near sinks, where occasional splashes may occur.
3. IP65 – Water Resistant:
- Complete protection against dust and water jets from any direction.
- Suitable for outdoor use, such as under-eave lighting or garden paths.
4. IP67 – Immersion Proof:
- Complete dust protection and protection against immersion in water up to 1 meter for 30 minutes.
- Perfect for areas exposed to heavy rain or temporary submersion, such as poolside or water features.
5. IP68 – Submersion Proof:
- Complete dust protection and protection against continuous submersion in water beyond 1 meter.
- Ideal for underwater installations, such as in ponds, fountains, or swimming pools.
Understanding these ratings helps you choose the right LED strip lights for your specific needs, ensuring that your installation is safe, reliable, and long-lasting.
Choosing the Right Waterproof LED Strips
When selecting waterproof LED strip lights, it is crucial to understand the differences between the various IP ratings to ensure you choose the right product for your specific needs. Two of the most commonly used ratings for waterproof LED strips are IP65 and IP68. In this section, we’ll explore the differences between these ratings and the best applications for each type.
IP65 vs. IP68:What’ss the Difference?
1. IP65 – Water Resistant:
- Protection Level: IP65-rated LED strips are designed to offer complete protection against dust and low-pressure water jets from any direction. This means they are highly resistant to dust and can withstand exposure to rain or splashes of water, making them ideal for outdoor use where direct water contact is minimal.
- Construction: Typically, IP65 LED strips are coated with a silicone or epoxy layer, which provides a protective barrier against water and dust while allowing the strips to remain flexible for easy installation.
- Usage: IP65 strips are best suited for applications where the lighting may be exposed to the elements but not submerged in water. This includes outdoor lighting for patios, pergolas, pathways, and under-eave installations. They are also suitable for indoor areas like kitchens and bathrooms, where occasional splashes may occur, but immersion is unlikely.
2. IP68 – Submersion Proof:
- Protection Level: IP68-rated LED strips offer the highest level of protection, with complete dust ingress protection and the ability to withstand continuous submersion in water beyond 1 meter. These strips are designed for environments where the lighting will be exposed to heavy water contact or submerged for extended periods.
- Construction: IP68 LED strips are often fully encased in a waterproof resin or silicone sleeve, providing robust protection that ensures the strips can operate efficiently even when submerged. This design also makes them slightly less flexible compared to IP65 strips, but it offers superior water resistance.
- Usage: IP68 strips are ideal for applications where the lighting will be exposed to heavy rain, submerged in water, or installed in areas with high moisture levels. Typical uses include underwater lighting for swimming pools, fountains, ponds, and water features. They are also suitable for areas that experience frequent flooding or need to withstand extreme weather conditions.
Best Applications for Each Type
IP65 – Best Applications:
- Outdoor Lighting: This type of lighting is perfect for illuminating gardens, walkways, and building exteriors where the lights may be exposed to rain or dust but not submerged.
- Patios and Pergolas: Ideal for creating a cozy outdoor ambience without worrying about occasional rain or humidity.
- Under-eave lighting is excellent for adding security or accent lighting to your home’s exterior. The strips are protected from direct water exposure but still need to withstand the elements.
- Kitchens and Bathrooms: These are suitable for under-cabinet lighting or accent lighting in areas where splashes or steam might be present.
IP68 – Best Applications:
- Swimming Pools and Fountains: Designed for continuous submersion, these strips are perfect for adding stunning lighting effects to pools, fountains, and other water features.
- Ponds and Water Gardens: Ideal for creating a magical underwater glow in ponds, highlighting fish, plants, and decorative elements.
- Harsh Outdoor Environments: Suitable for installations in areas that experience extreme weather conditions, such as heavy rainfall, snow, or frequent flooding.
- High-Moisture Areas: These are excellent for use in environments with constant high humidity or where the lights will be in direct contact with water for extended periods.
Common Uses of Waterproof LED Strip Lights
Waterproof LED strip lights are incredibly versatile and can be used in a variety of settings, both indoors and outdoors. Below are some of the most common applications where these durable and water-resistant lighting solutions can truly shine.
1. Outdoor Lighting (Gardens, Patios)
Waterproof LED strip lights are a popular choice for enhancing outdoor spaces. Whether you’re looking to illuminate your garden, patio, or pathway, these lights provide both functionality and ambiance.
- Gardens: Use waterproof LED strips to outline garden beds, highlight trees and shrubs, or create a glowing border along walkways. They can also be used to light up garden features like statues, water fountains, or rockeries, adding a magical touch to your outdoor space.
- Patios: Install LED strips under the edge of your patio or deck to create a soft inflow that’s perfect for evening gatherings. You can also use them to highlight architectural features, such as pergolas, trellises, or seating areas, adding both style and safety to your outdoor living space.
- Pathways and Driveways: Waterproof LED strips are ideal for lighting up pathways and driveways, enhancing visibility and safety. Their weather-resistant design ensures they can withstand rain, snow, and dust, making them a reliable choice for year-round outdoor lighting.
2. Bathrooms and Kitchens
Bathrooms and kitchens are areas where waterproof LED strip lights excel due to their resistance to moisture and splashes.
- Bathrooms: Add a touch of luxury to your bathroom with waterproof LED strips. They can be installed under cabinets, around mirrors, or along the baseboards to provide soft, ambient lighting. These strips are perfect for creating a relaxing atmosphere for evening baths or early morning routines. For added safety and style, consider installing them around the edges of your bathtub or shower, as long as the strips are rated for high moisture environments.
- Kitchens: In the kitchen, waterproof LED strips are a practical and stylish solution for under-cabinet lighting. They provide bright, focused light for food preparation areas, making it easier to chop, cook, and clean. Additionally, they can be used to illuminate kitchen islands, accentuate open shelving, or highlight backsplashes, adding both functionality and flair to your culinary space.
3. Pool and Underwater Lighting
For those looking to add a dramatic effect to pools, ponds, or other water features, IP68-rated waterproof LED strip lights are the perfect solution.
- Swimming Pools: Waterproof LED strips can be installed along the perimeter of your pool or even submerged within the water to create stunning lighting effects. Use them to highlight the pool’s edges or steps, ensuring safety while adding a vibrant glow that transforms your pool into a captivating nighttime oasis.
- Ponds and Water Gardens: Illuminate your pond or water garden with waterproof LED strips to showcase fish, plants, and other underwater features. These lights can be placed around the edge or directly within the water to create an enchanting underwater glow.
- Fountains and Waterfalls: Add dynamic lighting to fountains or waterfalls with submersible LED strips. The continuous, vivid illumination will enhance the natural beauty of the water feature, making it a focal point in your garden or outdoor space.
Waterproof LED strip lights are a versatile and durable solution for a wide range of applications. Whether you’re enhancing your outdoor spaces, adding functional lighting to your kitchen or bathroom, or creating a mesmerizing underwater light show, these strips offer the perfect blend of style and practicality. With the right waterproof LED strip lights, you can illuminate any space, indoors or outdoors, with confidence and creativity.
Explore MyLikeLed’s selection of waterproof LED strip lights and discover how you can elevate your lighting projects to the next level.
Installation Guidelines for Waterproof LED Strip Lights
Proper installation is crucial for maximizing the lifespan and effectiveness of your waterproof LED strip lights, especially in environments exposed to moisture, water, or harsh weather conditions. Below, we provide detailed guidelines to help you prepare the area for waterproofing and ensure proper sealing and protection of your LED strips.
1. Preparing the Area for Waterproofing
Before installing a waterproof LED strip, it is essential to prepare the area properly to ensure optimal performance and durability.
- Clean the Surface: Start by thoroughly cleaning the surface where the LED strips will be installed. Dust, dirt, and grease can prevent the adhesive backing from sticking correctly, which may compromise the waterproofing. Use a mild detergent or alcohol-based cleaner to wipe down the area, and ensure it’s scorched before proceeding.
- Check for Moisture: Ensure that the installation area is dry and free from any moisture. If you’re installing the strips in a damp environment, such as a bathroom or outdoor area, wait for a dry day to carry out the installation to avoid trapping moisture under the strips.
- Measure and Plan: Measure the area carefully to determine the length of the strips you’ll need. Plan the placement of the strips and the location of the power source. Consider how the strips will be connected and where the power supply will be housed to ensure easy access while keeping it protected from water exposure.
- Consider Ventilation: In enclosed spaces, ensure there is adequate ventilation around the LED strips to prevent overheating. Although LED lights produce less heat than traditional bulbs, proper ventilation is still essential for maintaining their longevity and performance.
2. Ensuring Proper Sealing and Protection
Proper sealing is vital to maintaining the waterproof integrity of your LED strip lights. Here to ensure that your installation is thoroughly protected:
- Use Waterproof Connectors: If you need to cut and reconnect LED strips, be sure to use waterproof connectors. These connectors are specifically designed to maintain the strips’ waterproof rating, preventing water ingress at the connection points. Ensure that the connectors are compatible with the strips’ IP rating (e.g., IP65 or IP68).
- Seal the Ends: The ends of the LED strip lights are vulnerable points where water can enter. To protect these areas, use silicone end caps and seal them with a waterproof silicone adhesive. Apply the glue evenly around the cap and the strip’s end to create a watertight seal.
- Apply Additional Waterproofing: For installations in extremely wet environments, such as underwater or in areas with heavy rainfall, consider applying an additional layer of waterproofing. Clear silicone sealant can be used over the entire length of the strip to enhance its water resistance. Make sure the sealant is evenly distributed and covers all exposed areas, including connectors and end caps.
- Secure the Power Supply: The power supply is another critical component that needs protection from moisture. If it’s not already waterproof, house the power supply in a waterproof enclosure. Ensure that the enclosure is sealed correctly and positioned in a location that is safe from water exposure. For outdoor installations, mount the power supply above ground level to prevent water from pooling around it.
- Test Before Final Installation: Before securing the LED strips permanently, connect them to the power supply and test the entire system to ensure everything is functioning correctly. This allows you to make any necessary adjustments before the adhesive backing is fully applied.
- Consider UV Protection: If you’re installing the LED strips outdoors, consider using a UV-resistant coating or housing to protect them from sun damage. UV exposure can degrade the materials over time, reducing their lifespan.
Maintenance Tips for Waterproof LED Strip Lights
Proper maintenance of your waterproof LED strip lights ensures their longevity and consistent performance, even in challenging environments. Here are some essential tips on how to clean and maintain your LED strips, along with advice on troubleshooting common issues like condensation.
1. How to Clean and Maintain Waterproof LED Strips
Maintaining your waterproof LED strips is crucial for keeping them in optimal condition and extending their lifespan. Here to keep your lights shining bright:
- Regular Cleaning: Dust, dirt, and debris can accumulate on the surface of the LED strips over time, potentially reducing their brightness. To clean them, use a soft, dry cloth to wipe away any dirt gently. For more stubborn grime, you can use a slightly damp microfiber cloth. Ensure that the fabric is not soaking wet, as excess water could seep into the connections, significantly if the waterproofing is compromised.
- Avoid Harsh Chemicals: When cleaning your LED strips, avoid using harsh chemicals or abrasive cleaning agents. These can damage the protective coating and reduce the effectiveness of the waterproofing. Stick to mild soap and water or an alcohol-based cleaner for safe cleaning.
- Inspect Regularly: Periodically inspect the LED strips for any signs of wear and tear, such as cracks in the silicone coating, peeling adhesive, or exposed wiring. Catching these issues early allows you to address them before they become serious problems, potentially preventing water ingress and extending the life of the lights.
- Check Seals and Connections: Over time, the seals and connectors of your waterproof LED strips may degrade, especially in outdoor or high-moisture environments. Regularly check these areas to ensure they are still secure and intact. If you notice any damage, reseal the affected areas with silicone adhesive or replace the connectors to maintain the waterproofing.
- Keep the Power Supply Dry: The power supply should be kept dry and free from moisture. If it’s located outdoors, make sure it’s housed in a waterproof enclosure and check the enclosure periodically for any signs of wear or water ingress.
2. Troubleshooting Common Issues Like Condensation
Even with proper installation and maintenance, waterproof LED strips can sometimes encounter issues such as condensation. Here to troubleshoot and resolve common problems:
- Condensation Inside the LED Strip:
- Cause: Condensation occurs when warm, moist air inside the strip comes into contact with a more excellent surface, leading to water droplets forming inside the protective casing.
- Solution: If you notice condensation inside the LED, it’s essential to address it promptly. First, turn off the power and allow the strip to dry completely. You can accelerate the drying process by gently warming the strip with a hairdryer on a low setting. Ensure that the strips are not overheated, as this can damage the LEDs.
- Prevention: To prevent future condensation, make sure all seals are intact and properly sealed. You may also consider placing the LED strips in a location with better ventilation or using a dehumidifier in the area to reduce moisture levels.
- Flickering Lights:
- Cause: Flickering lights can be caused by loose connections, a faulty power supply, or water ingress, which compromises the electrical components.
- Solution: Check all connections to ensure they are secure. If the flickering persists, inspect the power supply and replace it if necessary. If water ingress is suspected, dry the strip thoroughly and reseal any compromised areas.
- Dimming or Reduced Brightness:
- Cause: Reduced brightness can occur due to dirt accumulation on the strip, ageing of the LEDs, or water damage affecting the circuitry.
- Solution: Start by cleaning the strips to remove dirt or debris. If the issue persists, it may be due to the LEDs’ natural ageing or damage from moisture. In such cases, replacing the affected section or the entire strip may be necessary.
- Adhesive Peeling Off:
- Cause: The adhesive backing of LED strips may peel off over time, especially in humid or hot environments.
- Solution: Reapply the strip using a robust waterproof adhesive or double-sided tape designed for outdoor use. Ensure the surface is clean and dry before reapplying to ensure a secure bond.
Maintaining your waterproof LED strip lights is essential for ensuring they continue to perform well in all environments. By regularly cleaning the strips, inspecting them for signs of wear, and addressing issues like condensation promptly, you can keep your lights in excellent condition for years to come. Following these maintenance tips will help you avoid common problems and enjoy the full benefits of your waterproof LED strips.
At MyLikeLed, we’re committed to providing you with high-quality LED products and the best advice for keeping them in top shape. If you encounter any issues with your LED strips or need further guidance, don’t hesitate to reach out to our team for expert assistance.
Conclusion
Investing in durable and waterproof LED strip lights is a smart choice for anyone looking to enhance their lighting setup, whether indoors or outdoors. These versatile lights not only provide exceptional brightness and flexibility but also ensure long-lasting performance, even in challenging environments. By choosing waterproof LED strips, you’re protecting your investment from moisture, dust, and harsh weather conditions, ensuring that your lighting remains vibrant and reliable for years to come.
Proper installation and regular maintenance further extend the life of your LED strips, allowing you to enjoy their benefits with minimal hassle. Whether you’re lighting up a garden, brightening a bathroom, or adding ambience to a pool area, waterproof LED strips offer the durability and performance needed to create stunning lighting effects with confidence.
At MyLikeLed, we offer a wide range of high-quality, waterproof LED strip lights designed to meet your specific needs. Explore our collection today and take the first step toward a brighter, more beautiful space with lighting solutions that are built to last. Contact us today!
FAQs
Yes, you can use waterproof LED strip lights outdoors. Make sure you choose a strip with a high IP rating (like IP65, IP66, or IP68) to handle rain, humidity, and other outdoor conditions.
To install waterproof LED strip lights, clean the surface, peel off the adhesive backing, and stick the strip firmly in place. For added security outdoors, you might want to use mounting clips or channels.
Yes, waterproof LED strip lights can be cut, but you need to cut only at the marked points. After cutting, you’ll need to reseal the exposed end with waterproofing materials like silicone or special end caps to maintain water resistance.
No, waterproof LED strip lights usually use a standard LED power supply, but it’s best to use a waterproof power adapter if you’re setting them up outdoors to avoid any electrical hazards.
Waterproof LED strip lights typically last between 30,000 to 50,000 hours. Their lifespan can vary depending on the quality, how well they are installed, and the environmental conditions they are exposed to.

Hi, I’m Xylia Xiong, a sales professional with 14 years of experience in the LED strip light industry. I specialize in providing tailored solutions, leveraging my expertise in LED products and the latest industry trends. Known for effective communication and problem-solving, I’m dedicated to helping lighting manufacturers, importers, and distributors achieve their goals.
Let’s work together to create customized solutions that exceed expectations.
Related Posts
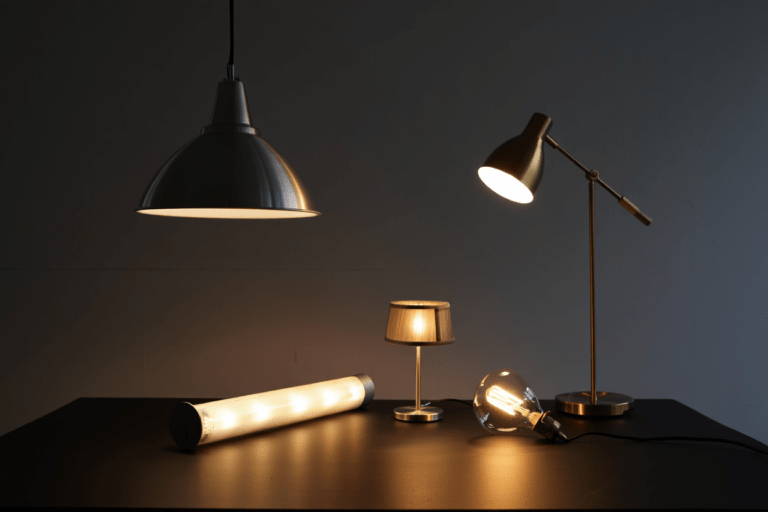
Types Of Lighting And Their Applications – Expert Guide
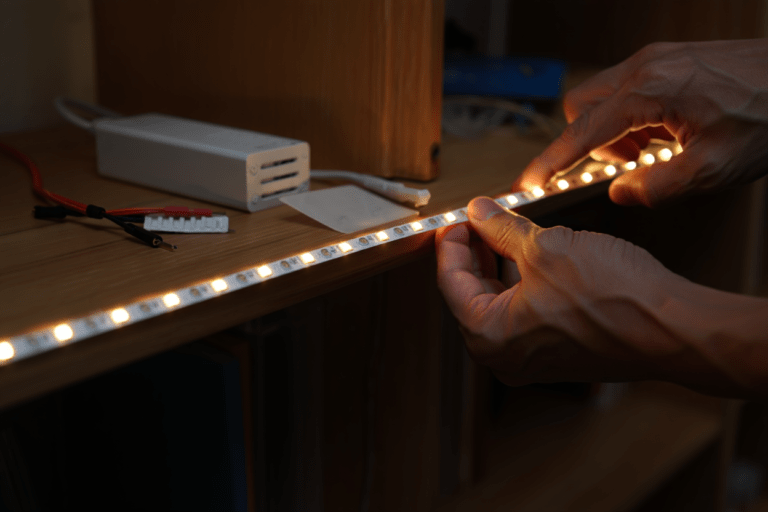
How To Make LED Strip Lights Brighter?
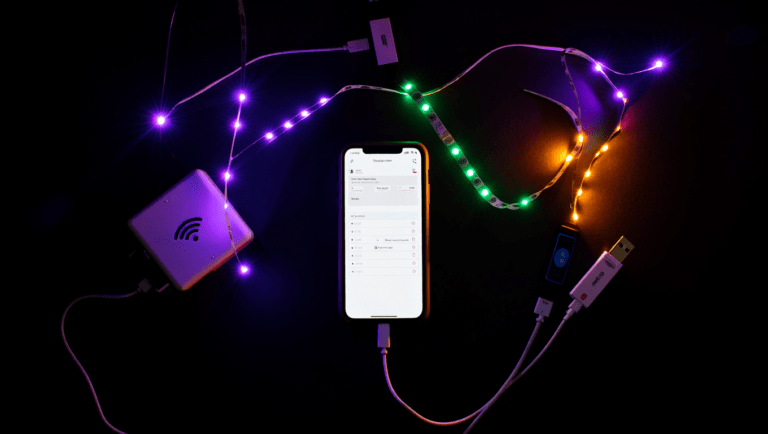

- Call Us: +86-15920391130
- Email: info@mylikeled.com
- Office Address: No. 4 Keying road, Beitai road, Baiyun district, Guangzhou, China
- Factory: Building 12, Liandong U Valley, Guangqing Industrial Park, Shijiao Town, Qingcheng District, Qingyuan City, Guangdong, China
Copyright © 2025 – My Like Led All rights reserved.