LED Heat Sink: Its Function and Significance
Table of Contents
The performance and longevity of LED fixtures can be significantly compromised due to overheating. Therefore, installing suitable heat sinks is crucial to ensure the proper functioning of LEDs and their thermal management system. But what exactly is a heat sink, and why is it vital for LEDs?
A heat sink is essentially a device that carries heat away from the LED light source. It acts as a guard against overheating, shielding the light from potential damage and consequently prolonging the lifespan of any LED.
Various LED heat sinks exist, but there’s no need to stress over the selection process, as this article will guide you. Let’s dive in and explore the world of LED heat sinks!
What does an LED Heat Sink entail?
An LED heat sink denotes a device responsible for taking in the heat emitted by the LED module and passing it onto the ambient air. It plays a crucial role in maintaining the LED’s temperature and preventing overheating scenarios. Its significance to any LED lighting system cannot be understated.
This heat sink is usually crafted from aluminum or other materials with good heat conductivity. It boasts a design of multiple fins and ridges designed to amplify its surface area, thus enhancing heat dispersion. The increased surface area enables heat to disperse more efficiently. The role of the LED heat sink is to draw heat away from the LED and transfer it to the surrounding air, ensuring the LED remains cool and operates optimally.
How was the Led heat sink made?
The manufacturing process of LED heat sinks involves several steps and primarily employs metals like aluminum or copper due to their excellent heat conductivity. Here are the general steps involved:
- Material Selection: The first step involves choosing the right material. Aluminum is often preferred due to its good thermal conductivity, lightweight properties, and cost-effectiveness. Copper is used in some high-performance applications as it has even better thermal conductivity but is heavier and more expensive.
- Designing: The design of the heat sink depends on various factors, such as the LED light’s Power, the operating environment, and the expected thermal performance. This can involve computational fluid dynamics (CFD) simulations to predict the heat sink’s performance under different conditions. The design often incorporates fins or other extended surfaces to increase the surface area, thereby improving heat dissipation.
- Manufacturing: Once the design is finalized, the heat sink is manufactured using techniques such as extrusion, stamping, casting, or CNC machining. The method chosen largely depends on the complexity of the design and the production volume.
- Extrusion: This is the most common process for making aluminum heat sinks. The aluminum is heated and forced through a die to create a shape with fins or other extended surfaces. This process is suitable for creating complex, cross-sectional profiles.
- Stamping: This method uses a die to stamp the heat sink shape from a metal sheet. It’s cost-effective for high-volume production but may not be suitable for complex designs.
- Casting involves pouring molten metal into a mold to form the heat sink. It’s useful for creating complex shapes but may not offer the same level of detail or finish as other methods.
- CNC Machining: This method uses computer-controlled machines to cut the heat sink from a solid metal block. It provides high precision and is suitable for complex designs but is more expensive and time-consuming than other methods.
- Finishing: The heat sink is finished to improve its aesthetic appeal and performance. This can involve anodizing (for aluminum heat sinks), which provides a protective last corrosion and increases surface emissivity and the radiative cooling effect.
- Mounting: The heat sink is ultimately attached to the device. This procedure must be performed in a manner that maximizes the thermal contact between the two components, often requiring the use of thermal paste or adhesive.
Remember, the purpose of an LED heat sink is to absorb and disperse the heat produced by the LED. Its objective is to prevent overheating and enhance the performance and lifespan of the LED. The design and manufacturing process of the heat sink is crucial for achieving these goals.
What Makes LED Heat Sinks Vital?
LED Heat Sinks are instrumental in safeguarding LED lights’ proper operation and extending their lifespan. These lights produce illumination via electroluminescence, a process that inevitably generates heat. This heat can harm the LED light’s internal components and decrease its efficacy and service life. An LED Heat Sink combats this issue by functioning as a cooling mechanism that dissipates the heat produced by the LED light, maintaining the internals at safe operational temperatures.
High thermal conductivity materials like aluminum are utilized in the design of the LED Heat Sink. These materials are excellent at rapidly and efficiently absorbing and dispersing heat. A large surface area facilitates maximum heat dissipation. Overheating can lead to LED lights becoming potential fire risks. Hence, the presence of an effective heat sink is essential.
The Functioning of an LED Heat Sink Explained:
The term LED heat sink describes the heat extraction mechanism from an LED light source through a heat sink. The mechanism operates in several phases:
- Heat Generation: As an LED light source is activated, it produces heat as a side-effect of light emission.
- Heat Transfer: The heat produced is channeled from the LED chip to the metal core printed circuit board (MCPCB) or the heat sink.
- Heat Dissipation: The heat sink forms a thermal bridge between the LED chip and the external environment, conducting heat away from the LED chip and into the atmosphere. The heat sink’s large surface area aids in providing ample room for heat dispersion.
- Heat Radiation: The heat sink projects heat into the surrounding environment through convection and conduction. Heat travels from the heat sink’s hot surface to the cooler air, establishing a temperature gradient that drives heat away from the LED chip.
- LED Cooling: As the heat radiates away, the LED chip’s temperature drops, thwarting overheating. This process allows the LEDs to function at a safe, efficient temperature. The heat sink also aids in averting damage to the LED chip that could result from excessive heat accumulation.
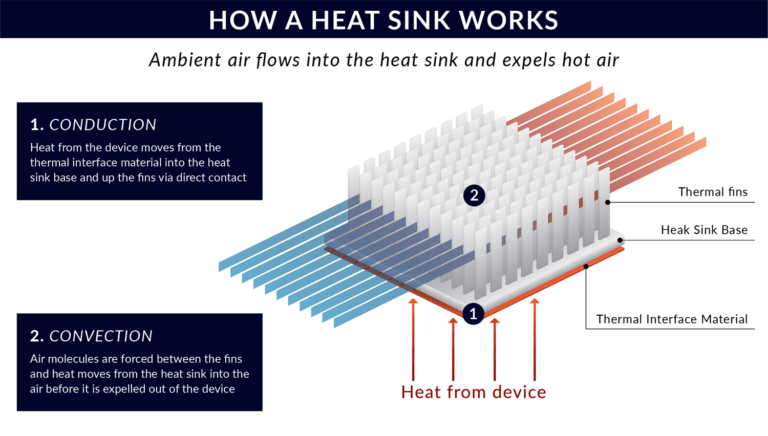
Varieties of LED Heat Sinks
Numerous varieties of LED heat sinks exist, encompassing active, passive, and hybrid models:
1. Active Heat Sink Variants
An active LED heat sink, a cooling mechanism, employs a fan or similar mechanical device to efficiently dispel heat from a light-emitting diode (LED) device, enhancing its performance and extending its lifespan. These active heat sinks prolong the LED’s life by mitigating the risk of overheating, which is why they are frequently employed in high-powered LED settings.
2. Passive Heat Sink Variants
Unlike active variants, passive LED heat sinks are structured to disperse heat generated by LED lights without necessitating fans or other active cooling systems. They depend on thermal conduction, convection, and radiation to transfer heat from the LED source into the environment.
These heat sinks are often crafted from aluminum or other materials exhibiting high thermal conductivity. They incorporate fins and other structures to increase the surface area available for heat transfer.
Not only are passive LED heat sinks durable and low maintenance, but they also offer low operating costs and noise levels, making them a go-to option for various lighting applications. Their resistance to weather and environmental conditions makes them ideal for outdoor lighting fixtures.
3. Hybrid Heat Sink Variants
Hybrid LED heat sinks to function as thermal management devices by fusing traditional metal heat sink materials with additional elements like heat pipes, vapor chambers, or phase change materials. These additional components enhance the heat dissipation capability of LED lighting systems. Their primary objective is to effectively eliminate heat generated by the LED chips, thus preventing thermal damage and boosting the performance and lifespan of the LED system.
4. Cold Plates
Designed specifically for LED lighting fixtures, cold plates work by dissipating heat from LEDs and maintaining optimal temperature levels. Crafted from aluminum, copper, or a blend of both, they conduct heat away from the LED and disperse it into the surrounding air. These systems are efficient, cost-effective, and lightweight.
5. Pin-Fin Heat Sinks
Comprising a metal base plate with several pins protruding from the surface, pin-fin LED heat sinks to enhance the surface area and boost heat dissipation. This design effectively manages heat from the LED source, thus controlling damage and augmenting performance. They are frequently used in applications requiring high-intensity and enduring lighting, such as street lighting, industrial lighting, and automotive lighting.
6. Plate-Fin Heat Sinks
Plate-fin LED heat sinks include a base plate, a series of fins, and a heat dissipation surface. The base plate, constructed from a highly thermally conductive material, is a secure platform for mounting the LED source. The fins increase the surface area for heat dissipation. These heat sinks are lightweight, easy to install, and cost-effective, making them a popular choice in lighting applications, particularly those that generate a lot of heat, such as automotive and industrial lighting.
7. Extruded Heat Sinks
Extruded LED heat sinks, crafted by extruding aluminum into a designated shape and size, serve to cool LED lighting fixtures. The finned structure increases the surface area for heat dissipation. When attached to an LED fixture, these heat sinks maintain the LED’s cool temperature, extending its lifespan. Their design renders them a cost-effective and customizable option, popularly utilized in commercial and industrial lighting.
8. Bonded Fin Heat Sinks
Composed of a base material and fins bonded together using a high-strength adhesive, bonded fin LED heat sinks enhance heat transfer efficiency and minimize thermal resistance. The fin design increases the heat sink’s surface area, allowing more heat to disperse into the air, keeping the LED lights cool, prolonging their lifespan, and maintaining their performance. These heat sinks, typically constructed from aluminum or copper, are used in various areas, including streetlights, indoor lighting fixtures, and automotive lighting systems.
9. Folded Fin Heat Sinks
Folded-fin LED heat sinks, used in LED lighting fixtures, are composed of thin metal fins that are folded and stacked together to create a large surface area for heat dissipation. This compact and efficient cooling solution is perfect for small LED lighting fixtures. The folded fin design promotes good airflow, enabling swift and efficient heat dissipation.
10. Z-Clip Retainer Heat Sinks
Designed with a Z-shaped clip, Z-Clip Retainer LED heat sinks are attached to the LED light to hold the heat sink in place, allowing for efficient heat dissipation. They help maintain the LED light at optimal temperatures, extending its lifespan. They also have an integrated LED light retaining system that prevents the LED light from loosening, enhancing safety.
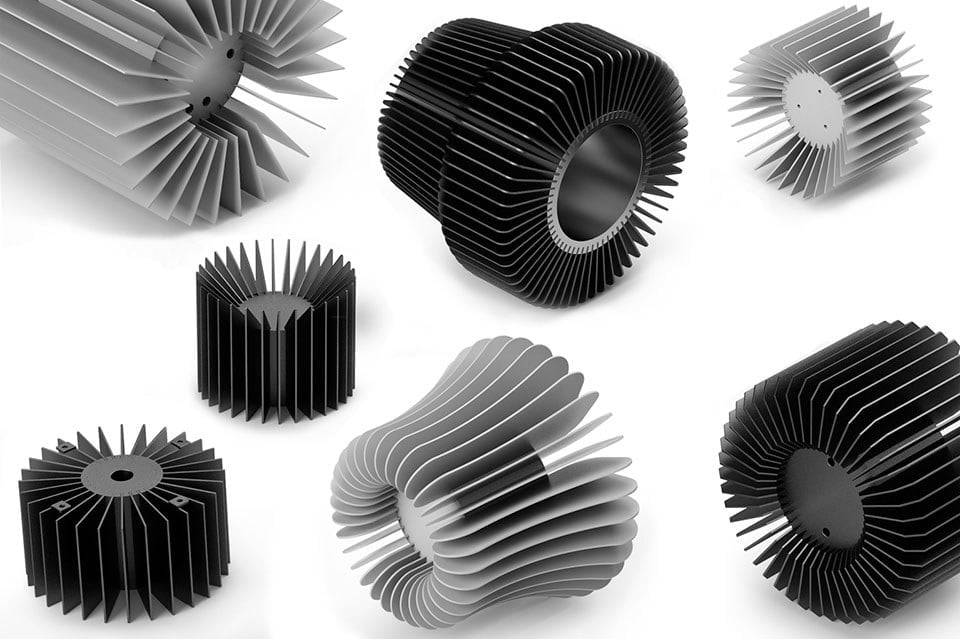
Different Varieties of Heat Sink Substances
Heat sinks are available in various substances, such as aluminum, copper, and polymer.
1. Aluminum-Based Heat Dissipation Solutions
Aluminum heat sinks for LED lighting are popular due to several major advantages. They are cost-effective, light in weight, and exhibit excellent thermal capabilities. These heat sinks, made of aluminum, facilitate rapid heat dispersion. This leads to a cooler operating environment for the system, thus enhancing its Efficiency. In addition, aluminum’s strong and durable properties make it well-suited to withstand severe environmental circumstances.
2. Copper-Constructed Heat Dissipation Solutions
LED Heat sinks made of copper are renowned for their superior heat dissipation. They help mitigate the risk of LEDs overheating and consequential damage. The high thermal conductivity of copper facilitates swift heat transfer away from the LED, ensuring its optimal functioning over extended durations. Furthermore, copper’s lightweight and corrosion-resistant attributes make it an excellent option for industrial utilization.
3. Polymer-Based Heat Dissipation Solutions
Polymer LED heat sinks offer enhanced heat dispersion, contributing to better efficiency and longer service life for LED products. Their unique polymer construction allows them to dissipate heat faster than traditional metal designs, thereby reducing the chances of LED malfunction due to thermal management challenges. Polymer LED products are also more energy-conservative, offering cost and energy efficiency.
Moreover, LED products equipped with polymer heat sinks demonstrate an extended lifespan compared to their counterparts without. This aspect can assist companies in diminishing their maintenance expenditures while boosting the durability of their LED lighting investments.
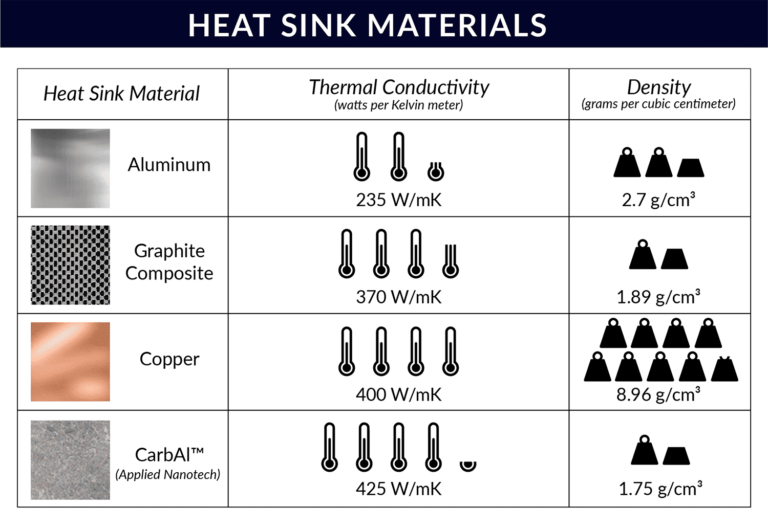
Choosing Between Aluminum and Copper for Heat Sink Materials: An Assessment
Each aluminum and copper possesses unique benefits and limitations. Consequently, comprehending their respective characteristics is pivotal to making a reasonable selection.
Aluminum Heat Sink | Copper Heat Sink |
Lightweight and low cost | Heavy and expensive compared to aluminum |
High thermal conductivity | High thermal conductivity |
Low mechanical strength | High mechanical strength |
Not as good at conducting electricity as copper | Excellent electrical and thermal conductivity |
Aluminum doesn’t conduct heat as effectively as copper, causing heat to travel more slowly. However, aluminum outshines copper in weight, is much lighter, and offers superior structural strength.
On the flip side, copper’s thermal conductivity surpasses aluminum’s, making it the preferred option for situations requiring efficient heat dissipation. Plus, copper doesn’t succumb to corrosion as aluminum does.
The choice between these two materials ultimately hinges on the specific application’s requirements. For instance, copper is a superior choice for industrial and automotive lighting. Meanwhile, for architectural lighting purposes, aluminum stands out as the ideal choice.
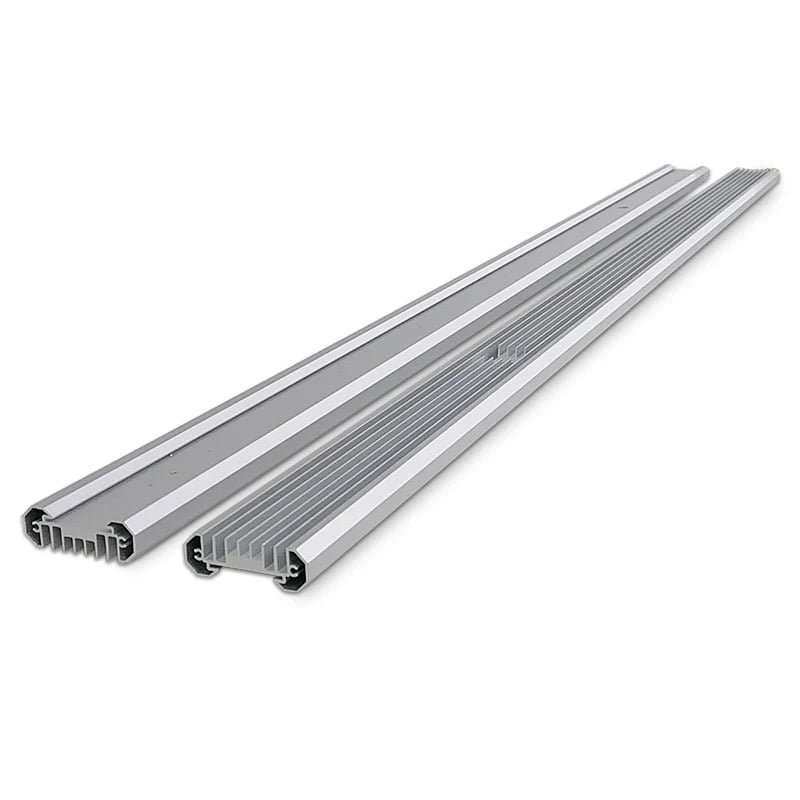
Considerations for Heat Sink Design
Formulating a heat sink design involves numerous aspects that must be considered. These elements include:
Heat Sink Varieties
The kind of heat sink used drastically influences the overall design elements. We have passive sinks, typically with an expansive surface area or fins, designed to diffuse heat via convection or radiation. On the other hand, active sinks involve fans or liquid cooling systems designed to remove heat from the source through the active displacement of air or liquid.
Each variety of sink carries its unique advantages and aspects to consider. For instance, active sinks could require additional Power for operation and generate more noise than passive sinks. Therefore, it is crucial to examine each type carefully.
Heat Sink Material Selection
The selection of heat sink material plays a significant role in determining the Efficiency and effectiveness of thermal management, as each material possesses distinctive thermal attributes.
Aluminum and copper are the most prevalent options due to their excellent thermal conductivity and large surface areas conducive to heat diffusion. Alternative materials such as ceramic or graphite may be needed to withstand higher temperatures. The shape and size of the heat sink also need to be considered to ensure peak performance and adherence to space limitations.
Designing Boundaries
The boundary design significantly affects the system’s cooling potential, cost, and Efficiency. Designers can fine-tune the thermal performance of the system through boundary design. The shape and size of the heat sink can influence factors such as airflow, convection, and conduction. Additionally, the boundary design plays a role in determining the surface area available for heat dissipation. A thoughtfully designed heat sink will have sufficient surface area to manage heat generation while minimizing costs.
Understanding the Role of MCPCBs in LED Heat Dissipation
Metal-core printed circuit boards (MCPCBs) are specifically engineered to draw heat away from the LED light source effectively. Serving as a thermal conduit, the metallic core of an MCPCB facilitates the transfer of heat from the LED to the heat sink.
The high thermal conductivity of metals, notably higher than that of FR4 (fiberglass-reinforced epoxy), allows the MCPCB to transfer heat away from the LEDs more efficiently. Besides, the metal core also bestows structural stability and enhances electrical connectivity, making it an ideal candidate for LED cooling solutions.
Do LED Strips Need a Heat Sink?
While small, less powerful LED strips generally do not need a heat sink due to their minimal heat generation, high-powered LED strips certainly benefit from one. A heat sink aids in heat dissipation, protecting the LED strip from heat-related damage.
Crafted from metal, heat sinks are effective conductors, drawing heat away from the LED strip and dispersing it into the ambient air. Without a heat sink, high-powered LED strips can overheat, diminishing lifespan and causing premature failure. Thus, for high-powered LED strips, a heat sink is advisable for ensuring their longevity and maintaining optimal performance.
Guidelines for Selecting an LED Heat Sink
The following are key elements to keep in mind when deciding on an LED heat sink:
Thermal Resistance
Thermal resistance characterizes the capacity of a heat sink to divert heat from the LED. High thermal resistance can lead to heat accumulation, resulting in premature LED failure due to overheating. However, a very low thermal resistance could mean an overly large heat sink, which may disrupt the overall design of the LED system. Finding the right balance between thermal resistance and other aspects like cost, size, and material is crucial to select the most suitable LED heat sink for your specific use.
Heat Dissipation
The heat sink’s primary role is to disperse heat away from the LED, preventing overheating and extending its lifespan. The LED could overheat and fail if the heat sink is ineffective in transferring heat. The heat dissipation should be evaluated considering the LED’s power output, ambient temperature, and the material’s thermal resistance. Selecting a heat sink with high thermal conductivity and low thermal resistance is advisable for optimal heat transfer. Proper heat dissipation ensures efficient and reliable cooling of the LED.
Thermal Conductivity
Thermal conductivity defines a material’s ability to transfer heat. A material with high thermal conductivity ensures efficient heat dispersion from the LED to the heat sink. However, different materials have varying thermal conductivity capacities. For instance, aluminum has a thermal conductivity of around 170-251 W/mK, while copper is higher, at approximately 401 W/mK.
Heat Sink Types
Passive heat sinks utilize natural convection and conduction to disperse heat, eliminating the need for active cooling methods such as fans or water cooling. This design can be attractive for certain applications, as it does away with maintenance, noise, and potential failure points associated with active cooling. Additionally, passive heat sinks can be more cost-effective and have a smaller form factor than dynamic cooling solutions.
Natural Convection
Natural convection is the heat transfer process through a fluid, usually air. The fluid or air flowing over the warm heat sink carries heat away into the environment. The design and structure of the fins on the heat sink can significantly enhance natural convection. Hence, it’s important to consider when choosing an LED heat sink.
Heat Dissipation Capacity
A heat sink with high heat dissipation capacity allows the LED lights to function at a lower temperature, reducing the risk of overheating damage and increasing the lights’ lifespan. This energy-efficient design reduces overall power consumption and long-term maintenance costs.
Fins’ Shape and Size
The size and number of fins affect the surface area available for heat dissipation. The shape of the fins can also impact the heat sink’s Efficiency. For instance, a heat sink with large, evenly spaced fins will likely offer superior heat dissipation compared to one with small, tightly packed fins.
How to Determine the Appropriate Heat Sink Size for Strip Lights?
Choosing the correct heat sink size for strip lights is vital for your lighting system’s longevity and efficiency. Below are the steps to follow:
Step 1: Ascertain the Power of the strip lights
The initial step is to identify the Power of the strip lights, usually measured in watts. This data is typically available in the product’s specifications.
Step 2: Compute the heat generated
Next, estimate the heat generated by the strip lights using the formula: Heat Generated = Power x Efficiency. The efficiency factor is generally around 90%.
Step 3: Identify the heat sink’s thermal resistance
Thermal resistance indicates the heat sink’s resistance to heat transfer, often expressed in °C/W.
Step 4: Establish the maximum allowable temperature increase
The maximum allowable temperature increase refers to the permissible temperature difference between the environment and the highest temperature the strip lights can reach, which is generally specified by the manufacturer.
Step 5: Calculate the necessary heat sink size
Finally, determine the required heat sink size using the formula Required Heat Sink Size = Heat Generated ÷ (Thermal Resistance x Maximum Allowable Temperature Rise).
Remember, these calculations provide only approximations. You may need to consult with a specialist for a more precise estimate. Additionally, consider the physical dimensions of the heat sink (length and width) to ensure its proper fit within your lighting system.
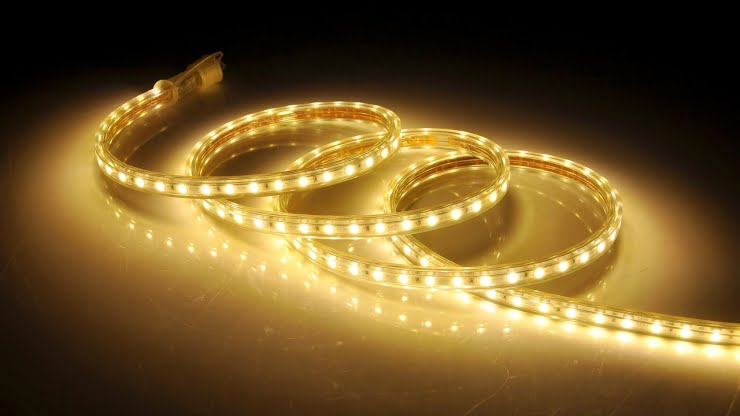
Installation Process for an LED Heat Sink
Follow the steps below to install an LED heat sink:
- Prepare the LED for heat sink installation. Securely place new LEDs into the holder or socket. If installed, ensure the LED is firmly in place to avoid dislodging during the installation.
- Clean the LED and heat sink surface with isopropyl alcohol for a solid bond. Then, apply a thin layer of thermal compound on the LED surface to enhance heat transfer between the LED and the heat sink.
- Position the heat sink with the LED and secure it to the holder or socket. Depending on the heat sink and LED holder design, this process may require screws, clips, or both. Once the heat sink is attached, please turn on the LED to confirm its correct operation. The LED should emit a steady, bright light without flickering or dimming.
- Once the LED is functioning correctly, secure any screws or clips. If required, apply an additional thermal compound to boost heat dissipation.
Optimizing the Performance of Your Heat Sink
Ensuring your LED heat sink is appropriately sized, well-constructed, and correctly installed is vital for maximizing Efficiency. The heat sink needs to be large enough to withstand the heat produced by the LED device. If it’s too small, the dissipation of heat becomes less effective. Choosing a high-quality material with excellent thermal conductivity is crucial for the heat sink’s performance.
Installation is another key aspect for optimal functioning. Securely attach the LED heat sink to your device, ensuring there are no gaps in the assembly that might hinder airflow. These measures will bolster the Efficiency of your LED heat sink.
Does the Heat Sink’s Weight Have an Impact?
Indeed, the weight of a heat sink is significant. A heavier heat sink tends to dissipate heat more effectively, thus keeping the components cooler. Increased weight generally implies more surface area, allowing the heat sink to absorb more heat from the components it cools. Hence, when selecting a heat sink, its size and weight are crucial considerations.
Final Thoughts
LED heat sinks are specially crafted for LED lighting. They maintain the optimum performance of LEDs while preventing excessive heat buildup. Transferring heat away from the LEDs keeps the devices cooler and functions more efficiently.
In essence, an LED heat sink averts potential damage caused by overheating. Without a heat sink, LEDs could not reach their peak performance. Hence, effective heat management is indispensable for any LED arrangement.
At MyLikeLed, we produce top-tier LED strips and LED neon flex. Our products undergo rigorous testing in advanced laboratories to ensure the highest quality. We also offer customizable options on our LED strips and neon flex. For superior quality LED strips and LED neon flex, reach out MyLikeLed without delay!
FAQs
LEDs produce heat at the base, and without a heat sink, this heat can damage internal components and reduce the lifespan and brightness of the LED.
A heat sink works by transferring heat away from the LED chip to the surrounding air through conduction and convection, keeping the LED cool.
Most LED heat sinks are made from aluminum or copper, as these metals are excellent thermal conductors and help in faster heat dissipation.
Not all, but high-power LEDs definitely need a heat sink to prevent overheating, while low-power or decorative LEDs may not require one.
Without a proper heat sink, the LED can overheat, leading to reduced brightness, color shifting, and a much shorter operational life.
Yes, in some cases, you can upgrade the heat sink to a more efficient one, especially in custom or high-performance LED setups, to improve cooling.

Hi, I’m Xylia Xiong, a sales professional with 14 years of experience in the LED strip light industry. I specialize in providing tailored solutions, leveraging my expertise in LED products and the latest industry trends. Known for effective communication and problem-solving, I’m dedicated to helping lighting manufacturers, importers, and distributors achieve their goals.
Let’s work together to create customized solutions that exceed expectations.
Related Posts
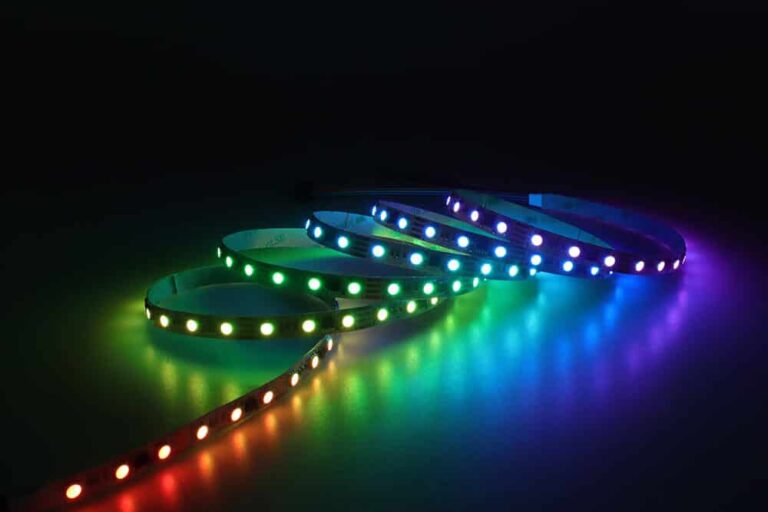
Comparing WS2811 Vs WS2812B: Key Differences

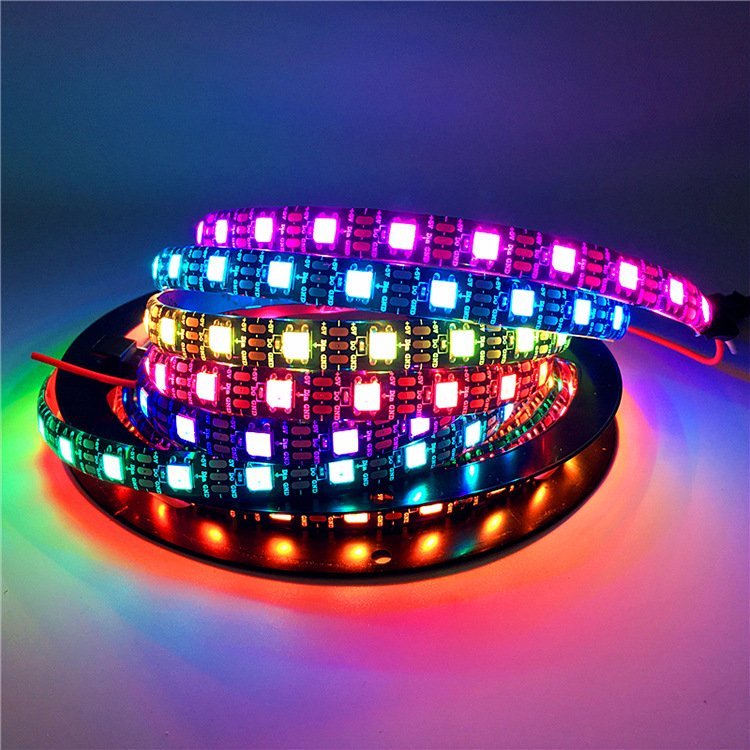
RGB Vs RGBW Vs RGBIC Vs RGBWW Vs RGBCCT LED Strip Lights

- Call Us: +86-15920391130
- Email: info@mylikeled.com
- Office Address: No. 4 Keying road, Beitai road, Baiyun district, Guangzhou, China
- Factory: Building 12, Liandong U Valley, Guangqing Industrial Park, Shijiao Town, Qingcheng District, Qingyuan City, Guangdong, China
Copyright © 2025 – My Like Led All rights reserved.